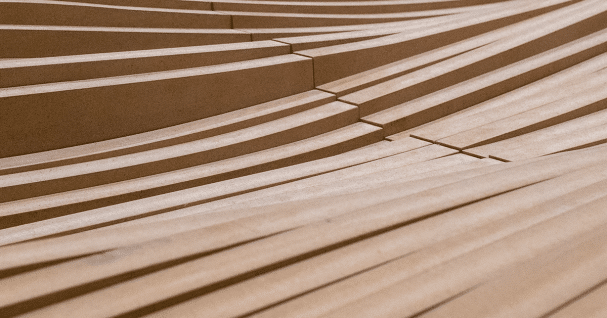
Medium-density fiberboard (MDF) is an extremely versatile building product, chosen for its strength, affordability, durability, and consistency. An engineered material, made by breaking down hardwood or softwood residuals into fine particles, combining it with wax and a resin binder, and pressing it with high temperature, MDF uses span a variety of home and professional projects, including:
- Furniture
- Cabinets and shelves
- Flooring
- Decorative projects
- Speaker boxes
- Wainscoting
- Doors and door frames
- Tradeshow booths and theater set construction
Advantages of MDF
- Generally more cost-effective than plywood or wood
- Is consistent throughout so doesn’t have voids or splinters
- Has a smooth surface that is perfect for painting
- Is easily cut with a router, scroll saw, band saw or jigsaw with no splintering, burning or tear-out
Disadvantages of MDF
- Takes in water and other liquids like a sponge and will swell unless well sealed
- Is very heavy
- Cannot be stained because it will soak up the stain, and has no wood grain for aesthetics
- Due to its makeup of small particles, doesn’t hold screws well
- Contains VOCs (eg. urea-formaldehyde) so needs special attention when cutting and sanding to avoid inhalation of particles
MDF comes in thicknesses from 1/4 in. to 1 in., but most home center retailers only carry 1/2-in. and 3/4-in. Full sheets are oversized by one inch, so a “4 x 8” sheet is actually 49 x 97 inches.
MDF Board Tips
When working with MDF (Medium-Density Fiberboard), there are several important tips to keep in mind to ensure your project is successful and safe.
Don’t use a hammer
MDF is extremely hard, so nails bend unless you pre-drill a hole, which is a bit impractical. Use a trim nailer to shoot nails into the surface, and a putty knife to scrape off the tiny bumps that result before filling the nail holes.
Don’t let MDF wood get wet
When exposed to water, MDF will swell to twice its thickness and will crumble if consistently exposed to water and damp conditions. There are moisture-resistant MDF products, that can be used in areas with humidity such as bathrooms and laundry rooms, but no MDF is waterproof.
Use solvent-based primer
The face of MDF is smooth, but the edges are fuzzy and need to be primed before painting to avoid a sandpaper effect. Most projects only require the edges to be sanded with 100-grit paper and primed with a solvent-based (not water-based) primer. When the primer dries, it can be sanded with 100-grit pads and wiped with a damp cloth before applying paint.
Protect your face
MDF work produces a sandstorm of fine, powdery dust that infiltrates everywhere and everything, so try to cut and rout MDF outdoors. If working indoors, drape sheets of plastic over furniture, doorways and air vents. Wear a tight-fitting dust mask and eye protection.
Keep an extra saw
MDF tends to dull saw blades quicker than most woods or plywood so have an extra saw blade handy.
Sand your edges
Cutting MDF creates sharp, open edges, so you will need to sand all cut edges, which can usually be accomplished with a fairly light-grit sandpaper, such as 150 grit.
Let our seasoned team be your guide. Contact us today to speak with our experts and uncover how specialized MDF types can elevate your woodworking or construction project to new heights!