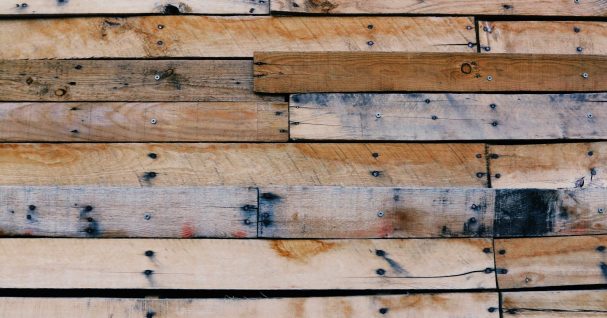
Plywood is created by gluing layers of thin veneers together, and delamination occurs when these layers separate. Although delamination can be caused by several factors, separation often occurs as a result of improper manufacturing processes. Today, we’re reviewing common signs of delamination as well as post-manufacturing causes of plywood separation and how to prevent them.
Signs Of Plywood Delamination
If you can inspect plywood before you buy it, you may be able to detect these common signs of delamination:
- Bubbles or lumps: A bubble or lump on the surface of the wood is a sure sign of delamination.
- Expanded edges: Delamination often occurs due to excess moisture. Swelling at the edges or corners of the plywood could indicate the wood was exposed to too much moisture and is beginning to delaminate.
- Blows: “Blows” are hollow spots inside the plywood. When too much moisture is present during manufacturing, moisture can turn to steam and create hollow cavities that usually can’t be seen until you cut into the wood. To check for blows, handle the wood and listen for a hollow sound.
How To Prevent Delaminated Plywood
Even if you buy high-quality plywood, delamination can occur over time if the wood is mistreated or exposed to high temperatures or moisture. Some of the most common heat- or moisture-related delamination issues occur because of:
- Improper nail/screw placement: Placing nails or screws too close to the edge can put too much pressure on the plywood and cause the exterior layers to bend up or down. This allows moisture to penetrate between the layers, causing delamination.
- Prevent it by: Placing nails and screws at least ¾ inch away from the plywood’s edges and corners.
- Leaks: Water from leaky windows, facets, or roofs can penetrate through carpet or linoleum, causing the plywood used to construct the house’s frame to become delaminated. In these cases, homeowners may be unaware of delamination until they find a lump beneath their flooring.
- Prevent it by: Shoring up any leaks in your home and vigilantly watching for any unusual bumps or lumps that may appear.
- Unvented areas: Unvented sections of your home, like an attic, can become hot and humid during the summer months. Without a vent to release excess moisture, the air becomes trapped. After prolonged exposure to moist air, the walls, floors, or even the underside of your roof may begin to delaminate.
- Prevent it by: Adding ventilation to areas that are exposed to high heat or excessive moisture.
Get High-Quality Plywood Today
If you’re concerned about purchasing delaminated wood, make sure you buy from reputable sources, like Forest Plywood. To ensure we provide our customers with the highest-quality products, we manufacture a wide range of lumber, flooring, and more at our in-house mill. Contact us today for materials, tips, and advice on your next woodworking project!