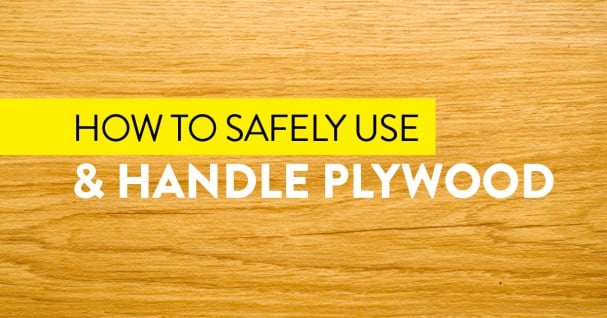
Typically sold in four foot by eight-foot sheets, handling plywood presents a bit of a challenge beyond the general safety procedures involved in any woodworking project.
Safely Hefting Around a Hulking Piece of Plywood
Part of what makes plywood such a great material is its sheer size. Unfortunately, that quality also poses one of its greatest challenges.
First, consider how much a sheet of plywood weighs. A full size sheet of ¾” hardwood plywood weighs in at about 55 pounds; some varieties weigh an additional 10 or 15 pounds. While many adults ably lift 55 pounds with only a moderate effort, handling the weight of plywood is complicated by its awkwardly large and unwieldy size.
The best method for moving plywood is teamwork. However, many do-it-yourself devotees take the “yourself” component to heart. For them, American Woodworker suggests the following options:
- Use a rolling cart to move plywood sheets
- Use a 12-foot-long rope to move sheets by tying loops on each end of the rope and then place the loops around the bottom corners of a sheet; then, pull up on the center of the rope for a “handle” and lift up (it will still be heavy, but a bit less awkward to move)
If project components do not require a full length of plywood, have it cut at the place of purchase prior to loading it up for the trip to the shop.
Cutting
Saws of all varieties pose serious safety risks. Working with a large material such as a sheet of plywood may increase the danger level. Individualism is a great thing, but, whenever possible, find someone to help in the cutting process, at least when first ripping the large sheet into smaller components.
However, if a project is a purely solo venture, be smart. All types of building jobs that involve saws and cutting warrant the use of both safety goggles and respirators. Be sure the saw is equipped with the proper blade for the material. If possible, use a rotary saw to make the initial crosscuts on plywood. Place the sheet atop sawhorses, or even a couple of 2 x 4’s set on the floor. You will get a more accurate cut than trying to do it solo using a table saw, have a higher chance of retaining all digits, and avoid long-term scarring using this method.
If a table saw is the only option available, use the appropriate safety devices:
- A sturdy out-feed table that supports plywood after it goes through the cutting blade area (larger shop carts with locking wheels may work, as do regular tables)
- Tables or sawhorses to provide side support when cutting wider pieces
- A featherboard for moving materials towards the sawblade that holds material up against the saw’s rip fence, decreasing the chances of kickback and bent sawblades
- A riving knife, properly used, may eliminate almost all kickbacks occurring during ripping, and when used with other proper safety practices such as correct blade heights, blade guards and stance, significantly deceases the risk of table saw injury
Dust
Most woodworkers wear eye protection that keeps dust and debris from their eyes. However, many disregard the need for lung protection. Cutting plywood creates dust. Inhaling dust particles from just about any substance can cause respiratory issues, from mild throat irritation, to asthma, or worse. Because the vast majority of woodworking occurs indoors, dust easily accumulates on surfaces and spews out from newly cut surfaces.
Dust remediation systems are one method of decreasing dust inhalation problems. Many tools come equipped with an attachment to a dust remediation system, or even to a simple shop vac. More elaborate systems that accommodate the needs of an entire shop also exist. However, one simple and widely available option is the dust mask, which is sold just about any place that also sells wood products. Read the label to ensure it is intended for use in wood shops and then WEAR IT.
Safety is Essential for Great Results
Adhering to safe plywood handling practices ensures great outcomes on all fronts. Shortcuts are tempting, and the added expense of safety implements may seem unnecessary, but in the end, they pay off.